OILFIELD SOLUTIONS THAT DELIVER SAFETY & SUSTAINABILITY
REPLACE OUTDATED TECHNOLOGY FOR A GREENER AND SAFER ENVIRONMENT.
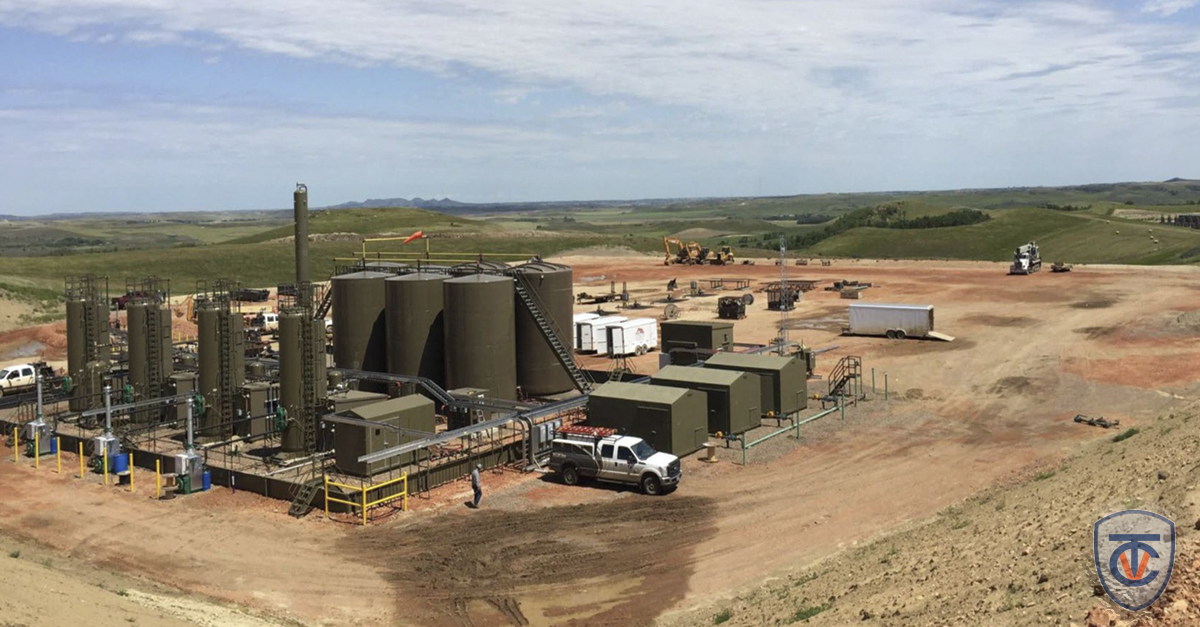
ARE YOU MEETING YOUR REDUCTION TARGETS?
CWT is an indirect heating system that is designed to heat crude oil for processing purposes. With GHG Emission reductions by 50% the CWT patented technology uses steam to indirectly heat crude oil, making it much safer, more cost effective, and better for the environment when compared to traditional firetube systems.
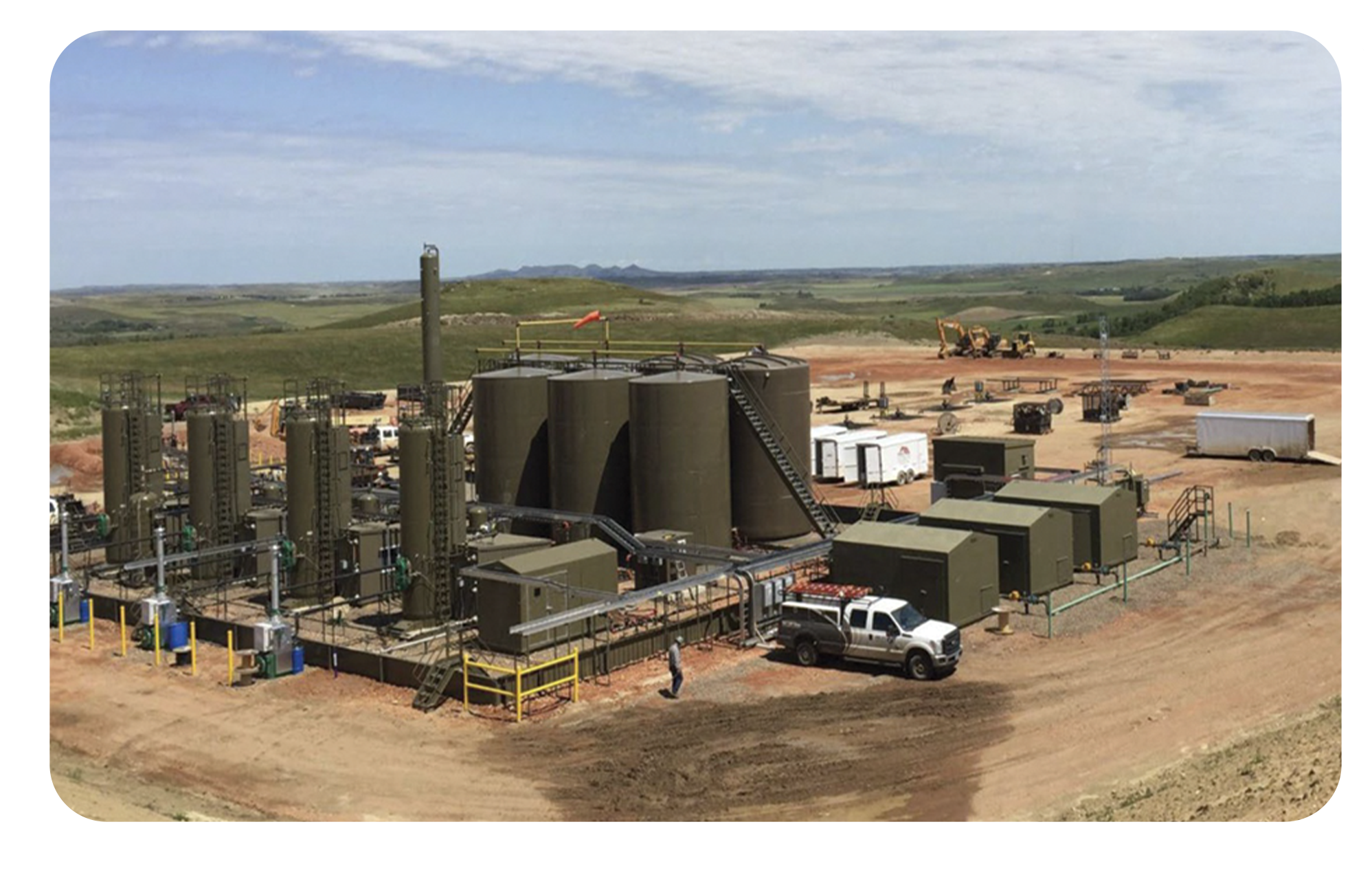
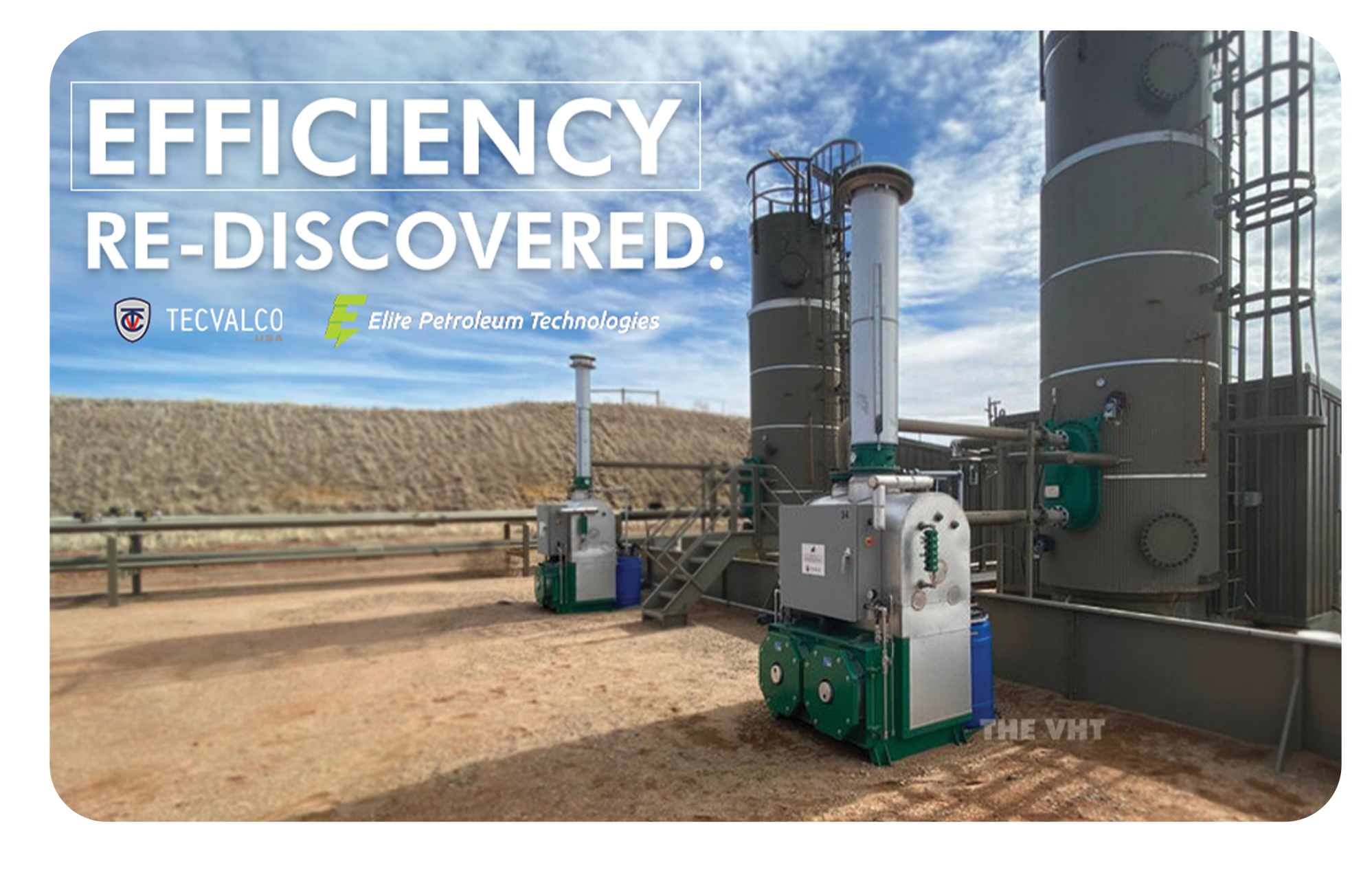
THE SAFER SOLUTION
The Tecvalco Heat Exchanger is perfectly suited to replace firetubes in any application. The Exchangers also offer a safer, more efficient means of heating oil compared to the traditional, dangerous, firetubes.
BENEFITS OF THE CWT HEATER TREATERS
CWT Heater Treaters are loaded with innovative technology to save you time and money in the field. With boiler life ranging from 45-50 years and heat exchanger life 15-20 years the Tecvalco CWT Heater Treater line of products is heat you can count on!
- Additional Benefits:
- No moving parts like motors or pumps.
- Virtually silent operation under 60dB
- Low pressure uses 2oz of well head gas or utility gas to operate.
- Reduces GHG emissions by up to 50%
- No electricity required to operate.
- Operates at 75-80% thermal efficiency
- Flame arrested air intake built to US Coast Guard Standard.
- Ability to lower water level in treater to treat more oil.
- Heat oil indirectly vs heating water to heat oil.
- A much greater ROI over the life of a well.
- Ability to retrofit existing locations. Plug and play.
- Eliminate firetube failures.
HOW IT WORKS
The CWT indirect heating system is a two-phase thermosiphon that transfers heat to process through an innovative technology called the Heat Driven Loop (HDL). A mixture of water and glycol is contained in a vacuum state and heated by a low pressure flame bed.
The water changes to steam at a lower temperature due to the vacuum state. The steam is then allowed to rush towards the process which requires the heat through a system of tubes (Heat Exchanger).
The steam then expands its energy and condenses back to liquid form. The liquid (Water) then gravity feeds back to the evaporation chamber where it will again be recharged back to steam. This continuous loop of transferring energy from a flame bed to process fluid, using steam and the latent heat of vaporization, is the key to the CWT system.
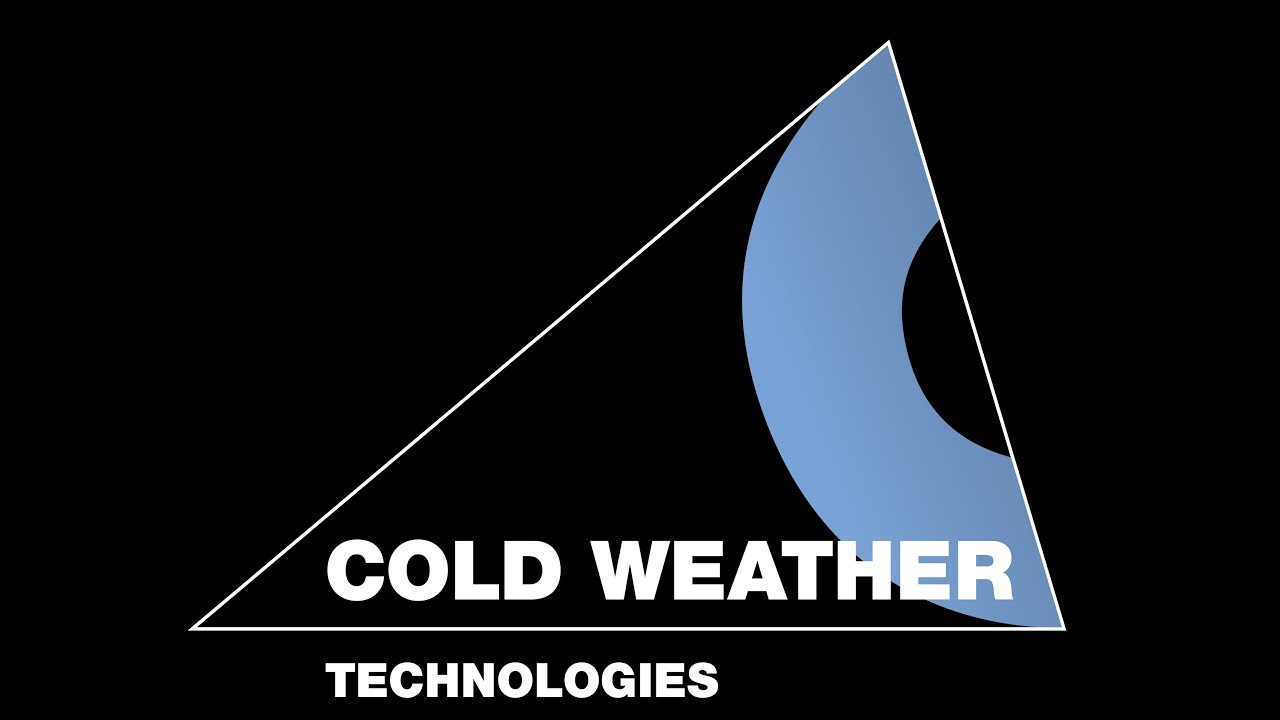
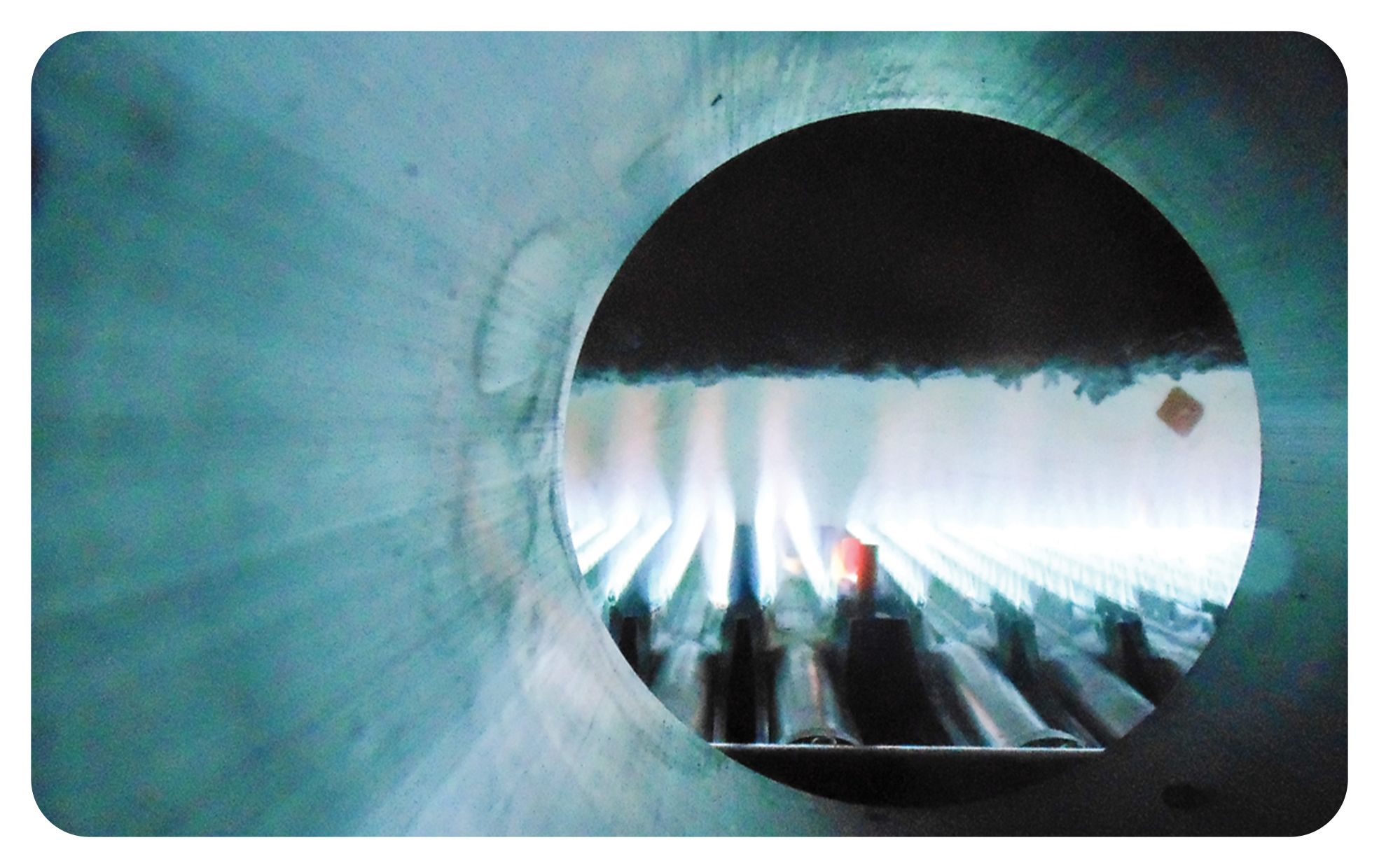
THE PROCESS SYSTEM
- Utilizes an ASME Sec IV Steam Boiler.
- Closed system under vacuum with no make-up water.
- Low pressure flame bed supplies heat to the water/glycol mixture causing the water to boil almost instanly which results in an exceptional response time.
- Uses a process line temperature sensor ensuring exact control.
- Steam temperature self adjusts to 250F.
- Uses the latent heat of vaporization making it more efficient.
- ASME Sec IV controls ensure safety.
HEAT EXCHANGER VS FIRETUBE
- The Tecvalco VHT Heat Exchanger is the perfect choice for your treater heating needs.
- Use of steam to heat the treater is a far safer alternative to traditional firetube methods.
- Heat exchanger can be placed directly into the oil reducing the energy and time required to heat the oil.
- Recognized by the NDIC as a safer alternative, granting a 21’ spacing exemption.
- Allows for a smaller lease site; saving costs on raw land, containment, less piping and insulation.
- Energy efficient with significant reductions in emissions and fuel consumption.
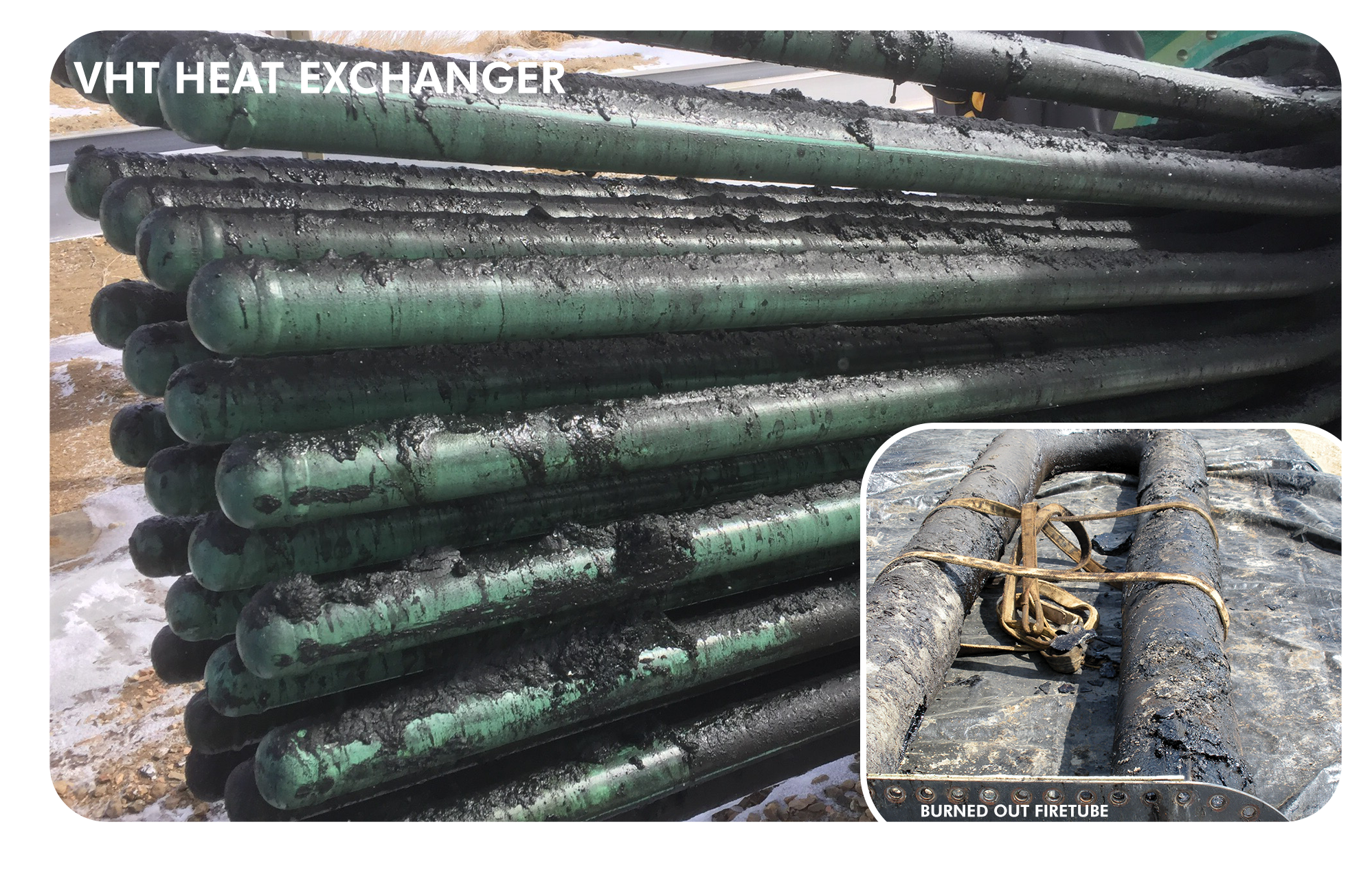
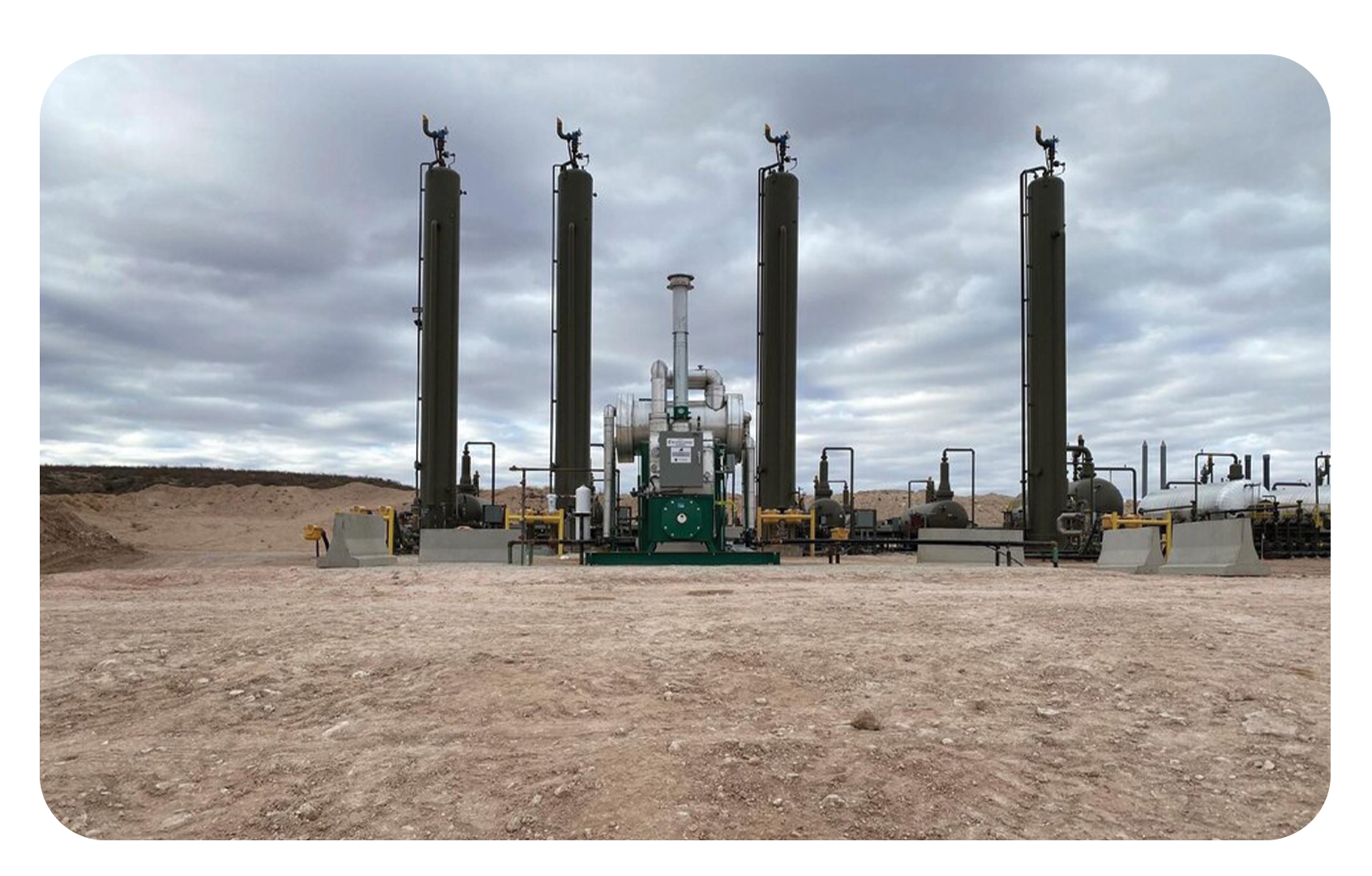
PRODUCT MODELS
The Tecvalco CWT Heater is perfectly suited to replace a fire tube in practically any application - but it is especially effective in those applications where fire tubes are restricted or prohibited.
The patented technology in Tevalco’s CWT Heater allows you to indirectly apply heat into applications and processes that restrict the use of combustion. This means you can do things such as: heat light oil on-site, reduce lease size with Tecvalco’s Two-Phase treating system, replace dangerous and costly fire tubes with innovative HDL technology, and much more.
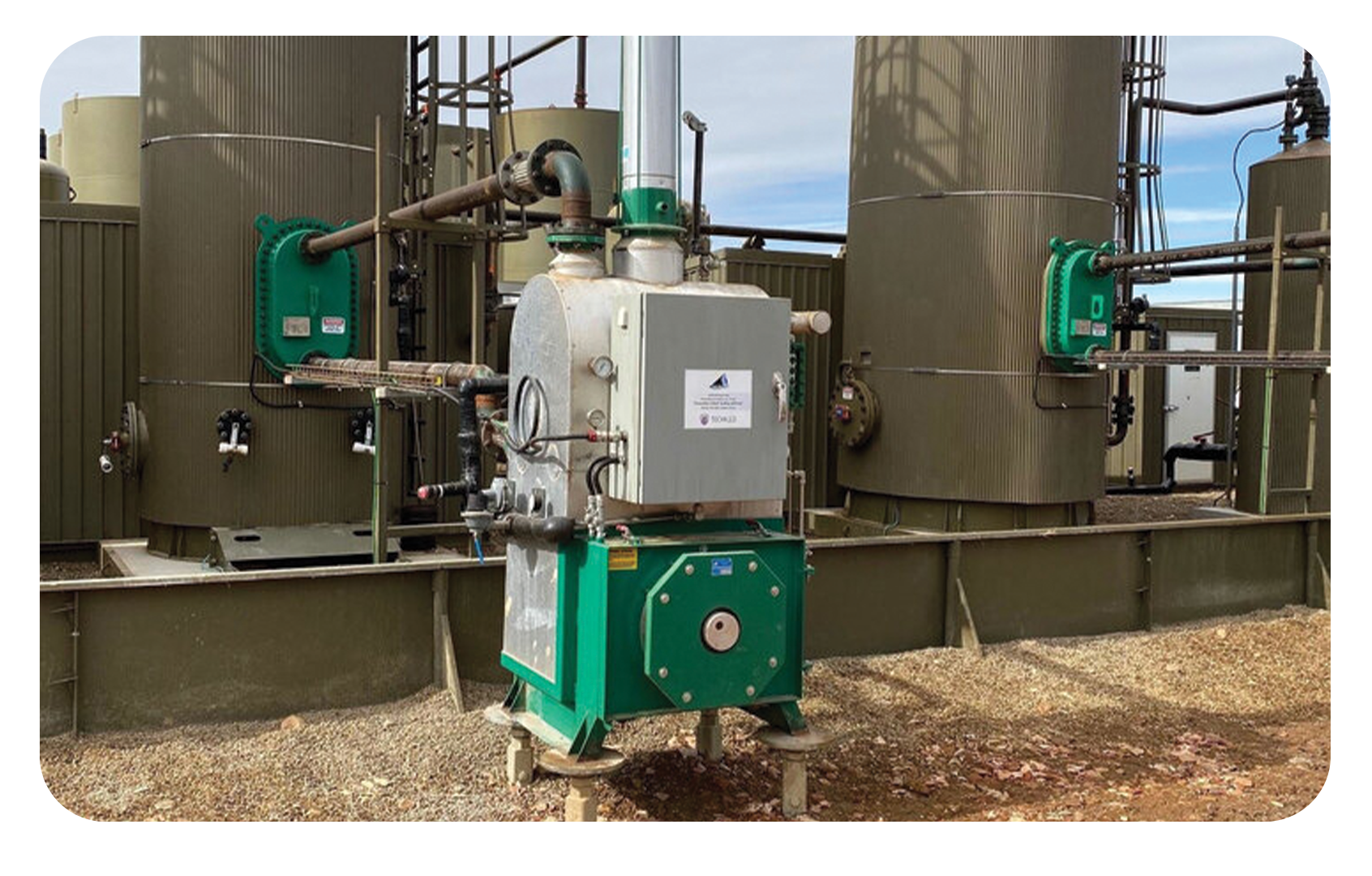
SINGLE + DUAL VHT
The CWT Heater facilitates the treatment of fluids on-site and can take oil to pipeline spec right in thetank. Through the application of heat with the CWTHeater, companies have seen water knockout cuts ofup to 26%, with 16.6% being the average volume ofwater removed from the fluid. Removing thatwater on-site greatly reduces the costs associatedwith treating facilities, disposal, and possible trucking.
Another exciting, new application for theCWT heater is in the Two-Phase Treater System. This technology uses a non-heated two-phase separator vessel rated at 125 psi. This vessel separates produced gases from the liquids coming from the well bore. Preferably, the gases are gathered - but they can also be sent to flare. Meanwhile, the liquids go to the process tank for oil-water separation, and then the oil goes to sales. This process tank is heated by the CWT Heating system which, along with retention time,encourages the oil and water to separate.
The CWT Heater is located in a general purpose location 21 feet away from the tank. This ensure ssafe operation of the heating system, yet allows the steam to very efficiently heat the process tank.This system eliminates: the vertical heater-treater,the unsafe direct-fired fire tube, and the need to heat large volumes of water. It also reduces lease size, and overall costs.
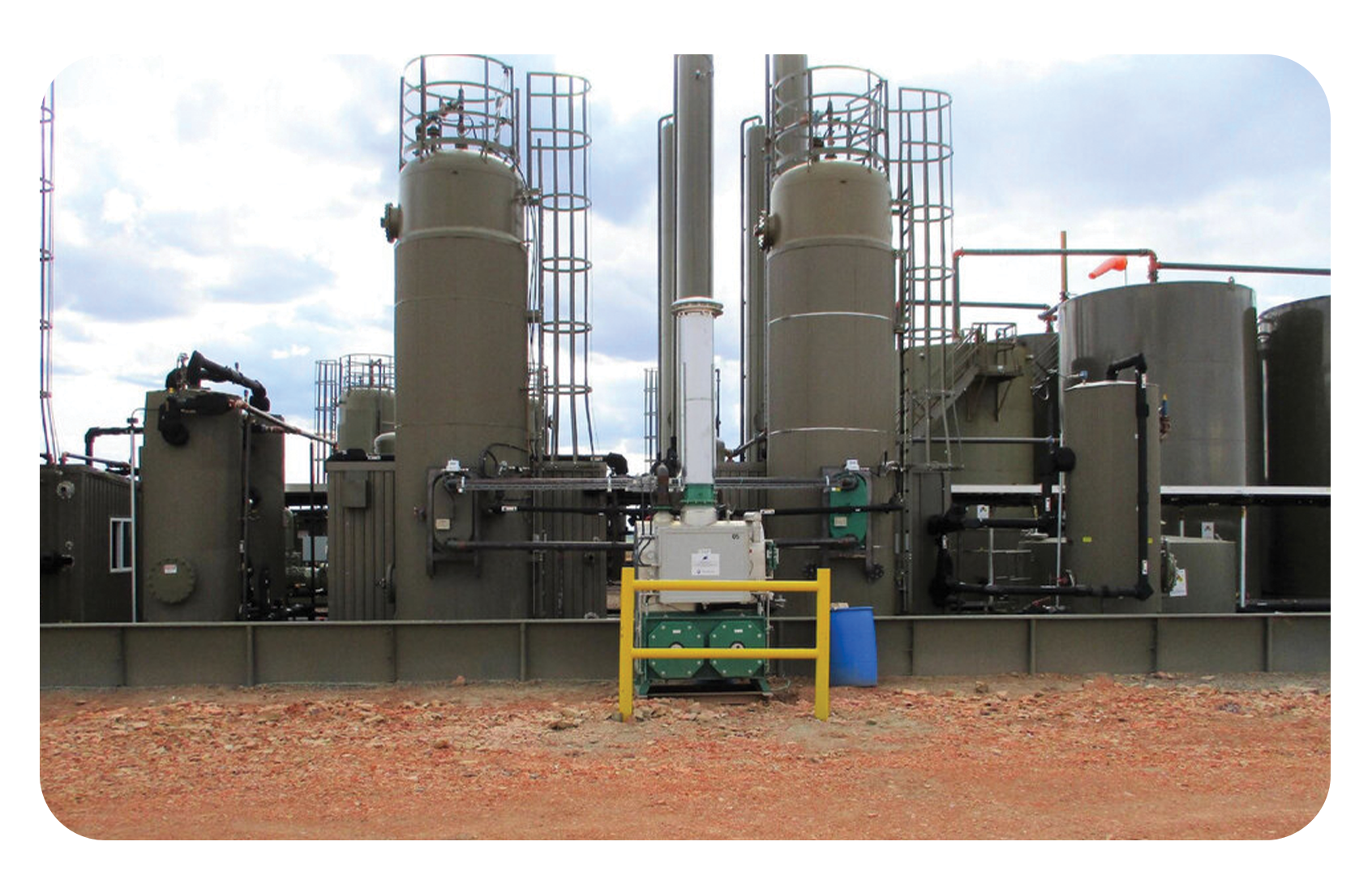
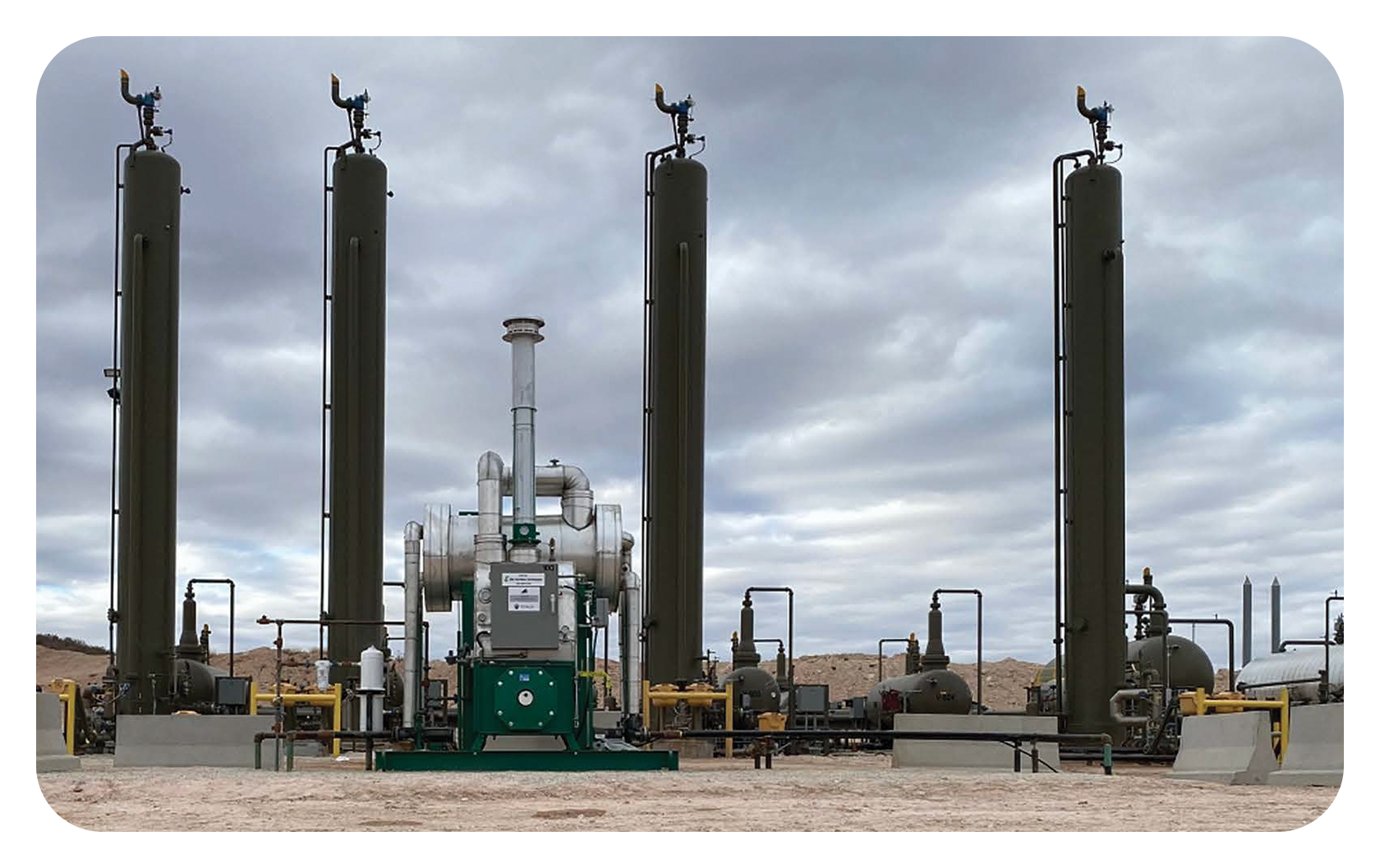
HORIZONTAL HEATER TREATER (HHT)
The Tecvalco CWT Heater is perfectly suited to replace a fire tube in practically any application - but it is especially effective in those applications where fire tubes are restricted or prohibited.
The patented technology in Tevalco’s CWT Heater allows you to in-directly apply heat into applications and processes that restrict the use of combustion. This means you can do things such as: heat light oil on-site, reduce lease size with Tecvalco’s Two-Phase treating system, replace dangerous and costly fire tubes with innovative HDL technology, and much more.
IN-DIRECT TANK HEAT
The Tecvalco CWT Heater is perfectly suited to replace a fire tube in practically any application - but it is especially effective in those applications where fire tubes are restricted or prohibited.
The CWT Heater facilitates the treatment of fluids on-site and can take oil to pipeline spec right in the tank. Through the application of heat with the CWT Heater, companies have seen water knockout cuts of up to 26%, with 16.6% being the average volume of water removed from the fluid. Removing that water on-site greatly reduces the costs associated with treating facilities, disposal, and possible trucking.
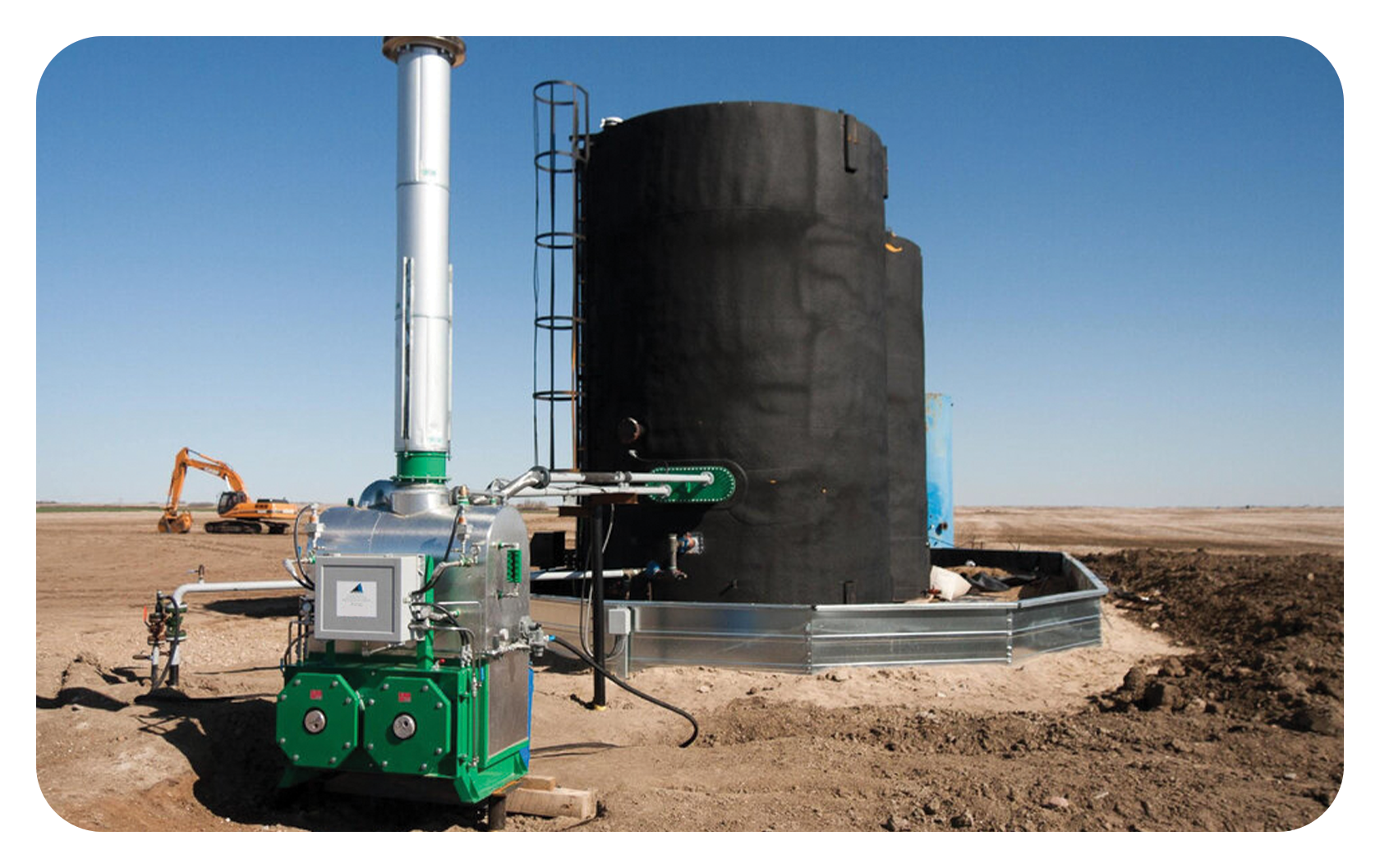
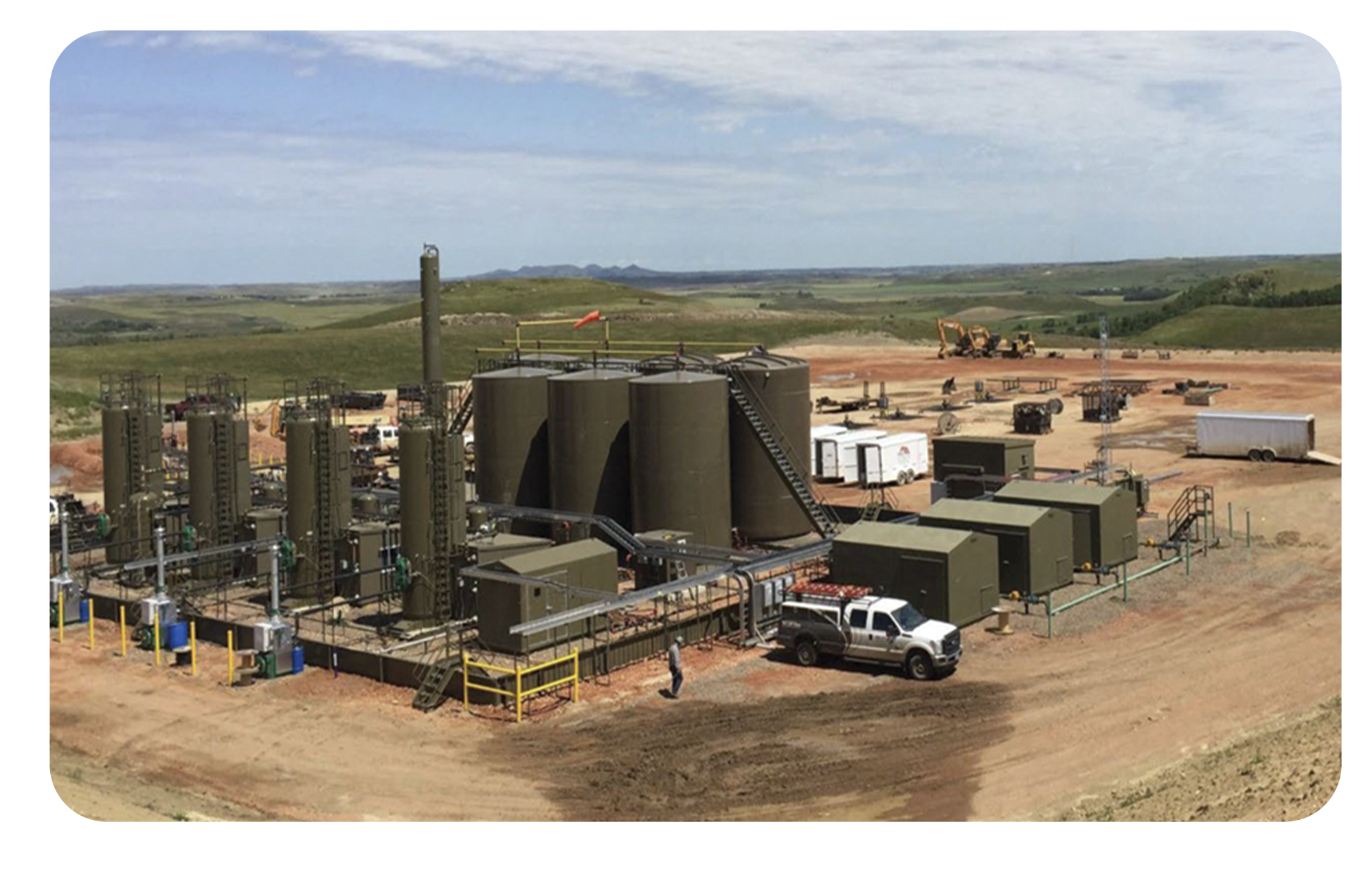
SMALLER PAD SIZE = ECONOMICAL SAVINGS
BENEFITS OF A SMALLER PAD SIZE
By utilizing the CWT indirect heating system oil producers will be able to significantly shrink their location (pad) size. This means there will be overall cost savings in the following areas:
- Production Equipment
- Less piping cost
- Less metal containment cost
- Less electrical cost
- Less labor cost
- Pad Size - Smaller Lease
- All raw land purchased
- Less dirt work (remediation)
- Cost and labor